中国软件智造未来——推动智能制造全链条革新
19429202025-03-12苹果软件11 浏览
在全球制造业加速数字化转型的背景下,中国正以软件技术为支点撬动智能制造的全链条革新。工信部数据显示,2023年我国工业软件市场规模突破3000亿元,智能制造试点示范项目生产效率平均提升45%。这场由软件驱动的产业变革,正在重构从研发设计到生产制造、从供应链协同到服务运维的完整产业生态,为"中国制造"向"中国智造"跃迁注入核心动能。
一、基础技术创新突破
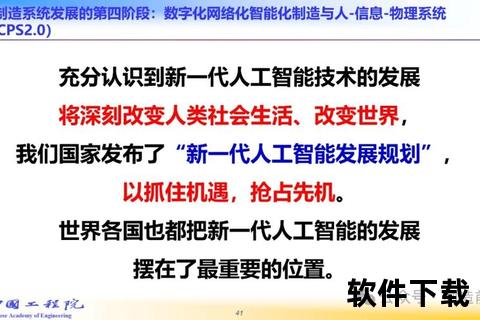
工业软件作为智能制造的"数字神经",正在经历从工具替代到系统重构的质变。华为FusionPlant工业互联网平台通过数字孪生技术,已实现90%以上工业场景的虚拟调试,将新产品研发周期缩短40%。沈阳机床i5智能系统深度融合运动控制算法与物联网技术,使设备联网率达到98%,加工精度提升至微米级。
人工智能与边缘计算的融合正在重塑生产决策体系。百度智能云打造的AI质检系统,在3C行业实现缺陷识别准确率99.5%,误检率低于0.1%。阿里云ET工业大脑通过时序数据分析,成功将光伏切片良品率提升7个百分点。中国工程院院士李培根指出:"软件定义制造的本质,是将物理世界的确定性转化为数字世界的可计算性。
二、产业链协同优化
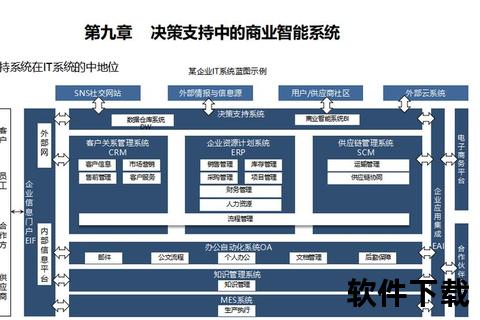
全链条数字化打通了传统制造的"信息孤岛"。长安汽车构建的协同研发平台,连接2000余家供应商实现BOM数据实时同步,使车型开发周期从36个月压缩至24个月。三一重工树根互联平台接入设备超80万台,构建的产业链画像系统可提前3个月预测市场波动,库存周转效率提升30%。
工业互联网平台正在重构制造服务模式。卡奥斯COSMOPlat赋能青岛啤酒打造柔性产线,实现从1000箱到10万箱订单的无缝切换,交付周期缩短50%。航天云网INDICS平台汇聚60余万家企业,通过产能共享机制使中小企业设备利用率提升35%。国家工业信息安全发展研究中心数据显示,平台化服务使制造业平均综合成本降低18.7%。
三、行业应用深化拓展
传统制造业的数字化转型呈现纵深发展态势。在纺织行业,恒力集团通过MES与ERP系统深度集成,实现从纱线到成衣的全流程追溯,订单响应速度提升60%。水泥行业的海螺集团应用智能控制系统,使吨熟料煤耗降低5公斤,年节约标煤超10万吨。赛迪顾问研究显示,流程工业的数字化改造平均节能达15%-20%。
新兴领域的技术融合催生创新业态。宁德时代依托数字孪生技术,将电池极片缺陷检测速度提升至0.15秒/片,量产一致性达到99.9%。大疆创新通过仿真软件迭代无人机设计,新产品试制次数减少80%。中国工程院院士周济强调:"软件不仅要解决'看得见'的生产问题,更要破解'看不见'的工艺know-how传承难题。
四、生态体系协同构建
产学研协同创新机制加速技术落地。清华大学与用友网络共建的工业软件联合实验室,已攻克CAD/CAE集成等12项关键技术。中控技术联合浙江大学开发的APC先进控制软件,在炼化装置应用使能耗降低3.5%。开源中国数据显示,工业领域GitHub开源项目年增长达120%,华为开源鸿蒙工业版已适配50余类工业设备。
人才培养与标准建设构筑发展根基。教育部"特色化示范性软件学院"已培养复合型人才2.3万名,但据工信部预测,2025年工业软件人才缺口仍将达80万。《智能制造能力成熟度模型》等12项国家标准陆续出台,为产业协同提供基准框架。中国信息通信研究院余晓晖院长指出:"构建自主可控的软件生态,需要技术突破、标准引领、人才培育的三维共振。
站在新一轮科技革命与产业变革的交汇点,中国软件正在书写智能制造的新篇章。从基础技术创新到产业链协同,从行业纵深发展到生态体系构建,这场全链条的数字化革新不仅关乎生产效率提升,更是制造范式变革的关键跃迁。未来需要持续加强核心工业软件攻关,完善开源协同创新机制,培育跨界融合人才梯队,方能在全球智能制造竞争中铸就中国优势,实现从"制造大国"向"智造强国"的历史性跨越。